TM70H DUO
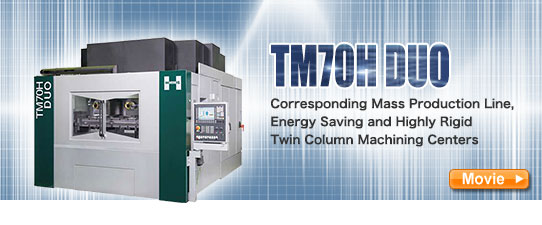

Feature
■ Energy Saving・Space Saving
■ High-Rigidity and Faster Acceleration/Deceleration
■ High Operation Ratio
■ High Maintainability
■ High Flexibility
■ High-Rigidity and Faster Acceleration/Deceleration
■ High Operation Ratio
■ High Maintainability
■ High Flexibility
Twin-Column Structure
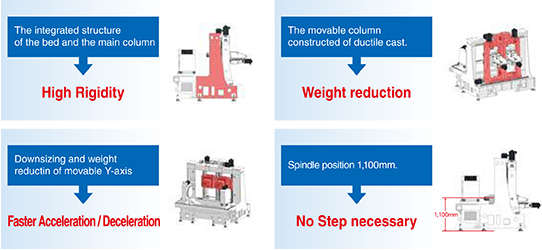
High Maintainability
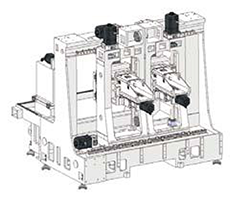
Since the drive unit is in the rear, main maintenance
can be done from the rear side.
No interference like fixture made quick maintenance possible.
Compensatable axes
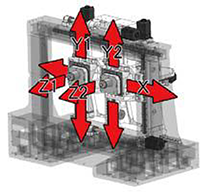
X axis : Spindle pitch adjusting mechanism
Y axis : Multi independent drive
Z axis : Multi independent drive
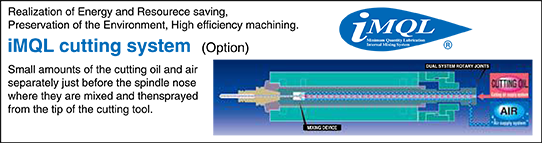
Specification
Item | TM70H DUO | |||
Spindle | Diameter | φ70mm | ||
Tool holder | HSK-A63 | |||
Spindle Pitch | 700mm | |||
Drive system | Direct connection (Coupling) | Built in Motor | ||
Bearing lubrication systen | Oil mist | Oil mist | ||
Max. rotation speed | 12,000min-1 | 20,000min-1 | ||
Drive motor | 10/7.5kw | 28.5kw | ||
Cutting fluid through spindle |
Coolant through spindle(MAX 7.OMpa) ★MQL |
|||
ATC | Tool change method | Direct | ||
Tool selection method | Fixed address, shortest path tool change method | |||
Tool storage capacity | 70 x 2 | |||
Max. tool diameter | φ7Omm(φl6Omm without adjacent tool) | |||
Max. tool length | 345mm | |||
Max. tool weight | 10.0kg | |||
Tool change time | TtoT | 1.2 sec | ||
Cto C (1/2 stroke) | 2.6 sec | |||
Feed unit | Rapid traverse rate | X axis | 62m/min < 6.9m/s2 > | |
Y axis | 62m/min < 6.9m/s2 > | |||
Z axis | 75m/min < 11.8m/s2 > | |||
Cutting feed rate | 1~10,000mm/min | |||
Travel | X axis | 650mm | ||
Y axis | 560mm | |||
Z axis | 530mm | |||
Reference pad | X,Y,Z axis | |||
Sliding parts | Linear guide(X・Y・Z axis) | |||
NC Device | SINUMERIK 840D sl(SIEMENS) | |||
Footprint (W x L) | 2,950mm x 5,025mm |
※★indicates options.